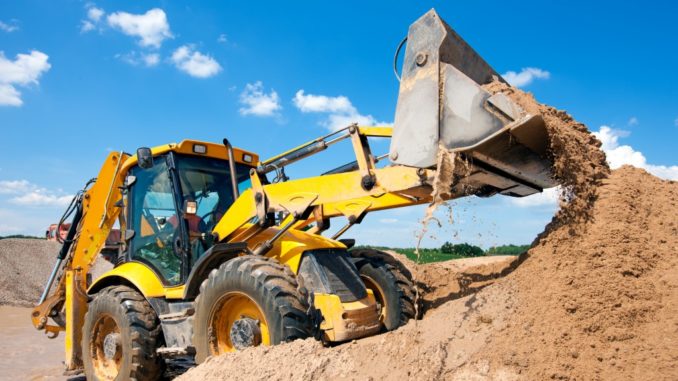
Machinery-dependent industries such as those in manufacturing and even automated food processing all have one weakness in common: machinery breakdown. Once a machine or equipment breaks down, not only is it expensive to repair (or may even require to be replaced entirely if it’s damaged beyond repair), but it can lead to downtime, lost production, or even fatal safety hazards. Even if a machine is down for just an hour, it can effectively halt the entire production line or overall operation (more so if it’s an integral part of the whole process), which can potentially cost a company hundreds of thousands, if not millions.
That said, you must avoid machinery breakdown at all costs and one of the best ways to do so by knowing the common causes of machinery breakdown and prevent them from occurring.
#1 Untrained Operator / Human Error
One of the most common, if not the most common, cause of machinery breakdown is human error and can occur even with brand new equipment. If the one operating the machine fails to follow protocol, lacks training, or didn’t read the user manual, the possibility for human error skyrockets, and your expensive and essential machinery ends up breaking down in the middle of its operation. There’s also the issue of lack of awareness or pure negligence, wherein even the best-trained operator in the facility ends up accidentally causing an error. And, as you can surmise, the best way to prevent this is to ensure that the ones operating your machinery are well-trained, qualified, and fit to do so. Although most machines nowadays have fail-safes and other breakdown mitigating features, it doesn’t always guarantee that failure can be prevented.
#2 Lack of Maintenance
This is pretty self-explanatory, but all machines experience wear and tear. Which is why regular maintenance is integral to ensure that the machine works at full capacity, and also to avoid breakdowns from occurring. It’s recommended to follow the owner’s manual as to how frequent a preventive maintenance routine should be done. Still, it’s also just as important to take note of the most common issues in the machines that need to be given more attention and more frequent inspection. If your machinery operates beyond the recommended operating period (to deliver a certain quota or to make up for lost production time after a repair), you may also want to adjust your maintenance schedule as well.
#3 Failure to Monitor and Replace Worn-out Components
Specific components are more susceptible to wear and tear and may need to be replaced as soon as signs of damage and wear shows up, and this can only be done if these parts are correctly monitored. It’s also just as integral to ensure that the spare parts used to replace the worn-out components are of high quality and the proper specifications as indicated in the manual. Some components may be hard to find or require to be fabricated, in which case you’ll want to have a list of suppliers for these specific parts on hand. For example, herringbone gears, which are used in many heavy pieces of machinery are known to be difficult to fabricate due to its design, so you should have already had the contact details of your local custom gear manufacturing company in Wisconsin ready in case a herringbone gear needs to be replaced.
#4 Poorly-Maintained Electrical Connections
Electrical problems are more of an external factor, but they are known to be one of the major factors attributed to machinery breakdowns. So you’ll want to ensure that all electrical connections to your machinery are just as well-maintained as the machinery itself.
Conclusion
Heavy machinery and equipment keep a manufacturing business running, which is why these machines must keep running, too. So take note of these top common causes of machinery breakdown to prevent them from occurring, and to ensure that your operations continue without a hitch.