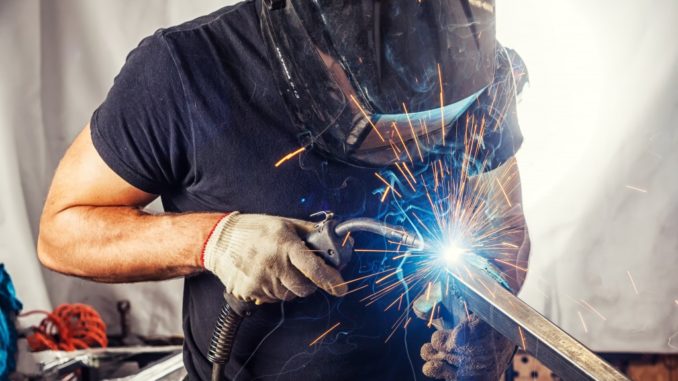
When you see monuments and metal roofing in Salt Lake City or wrought iron gates in Washington, as well as other metalwork around the U.S., have you ever been curious about the process that turned simple metals into those marvels?
Metal fabrication holds the key for any industry or project involving metal. The strictest definition places any process that involves shaping or cutting metal under metal fabrication. Anyone looking for custom metalwork will access any or all of the following metal fabrication services:
Design
This is the step where the product is conceptualized in a 2D and 3D format before they are fabricated. Engineers are usually in charge of creating designs for the metal product. Designing involves a lot of trial and error, learning what works and what doesn’t, and identifying what needs to be reconsidered for the product to work. Paper sketches and plans are often translated into computer software to simulate more problems that could not be done in actuality due to costs.
After the product is designed, metal fabrication plants begin to plan how these products will be manufactured. Plants either contract external design firms or tap into their internal department for these plans. These plans determine which procedures are required to be performed to finalize the products.
Build
Cutting, molding, shaping, and fabricating metals fit in this step. Plants determine the type of metal required by the project, which can range from stainless steel, copper, aluminum, and tin titanium, among others. Once the materials are chosen, they are brought into the shop for modification.
Metals that require reshaping are cast into molds, forged or hammered into new shapes, and cut with saw blades and power scissors. Contours are created in metal through nibbling, shearing, stamping, and punching. Pieces of metal are removed from larger chunks or sheets through machining or blanking.
Custom metalwork is also carved into shape through tuning or rotating metal workpieces while pieces are cut off; extrusion or the creation of cylindrical items from billets fed into dies, and drawing, the use of tensile force to draw molten metal into casting materials such as tapered dies.
Assembly
The final stage of the process is where shops finish and assemble components into their specified build. Units are either put together by hand or through machinery, though manual and automatic labor are both employed for certain assembly lines. Each piece is carefully protected from scratches and other damages. Replacing a part may be costly and time-consuming, especially if the piece is not easily replaceable.
Certain components require special treatment before and after assembly. Metals are treated with phosphating film, chromate, baking paint, and other treatments to strengthen and protect them against corrosion, oxidation, and other weather effects.
Materials are assembled in various ways. Adhesive bonding is enough for some pieces, while others require bolting, riveting, or welding. Parts of the finished product are sawn off to follow the specification. Metalwork is also polished, decorated, and painted before they are shipped.
Metal fabrication and the products that come from it are widely used in almost every industry, including construction, aerospace, energy, and shipbuilding. Homes with metal roofing in Salt Lake City, high-tech cars zooming down the roads of Seattle, and impressive statues in Tampa all owe their form and beauty to this practice. As cities expand, the value of metal fabrication will continue to grow.