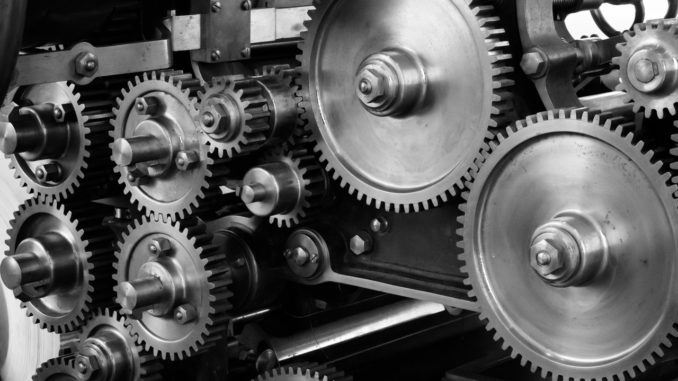
Machines are integral parts of the production process. That said, they need regular maintenance to stay in good working condition and avoid unexpected downtime that can, in turn, lead to unnecessary delays in production and higher overhead expenses.
However, not all types of maintenance are ideal in keeping machines in tip-top shape. Sometimes, maintenance personnel makes mistakes that are either doing more harm than good or not optimizing the performance of the machine altogether.
Whether it’s something small like a drilling machine or a bigger unit like a hot foil stamping machine, maintenance managers and service crew alike must avoid making these common machine maintenance mistakes.
1. Failure to complete documentation
Proper documentation of all maintenance tasks is imperative for every other task going to be done to the machine in the future. Maintenance personnel refers to history and previous documentation for the information they need to carry out their tasks, and if these pieces of information are missing or otherwise incomplete, it will take much more time and effort for them to perform maintenance tasks on the machine. As a result, downtime is extended, resources are wasted, and the risk of production delays is increased.
That said, every maintenance worker that performs tasks on a machine must document their work completely and correctly. Then, they must deposit their work log in a secure, central location where other maintenance personnel can easily access it for future tasks and troubleshooting. Maintenance managers can ensure that each of these steps happens for every task through proper training and strict implementation among their workers.
2. Not having replacement parts in stock
One of the biggest causes of extended downtime is the lack of a replacement part within the manufacturing plant. When maintenance staff has to call the manufacturer or set about looking for a replacement part somewhere else, this costs the company extra time and money, not to mention the potential revenue lost if the machine is a mission-critical one.
For this reason, all plants must keep a par stock of high-wear replacement parts. These are the parts that go through the most wear and tear and are most likely to need replacing. Mid-wear and low-wear parts are the ones that are unlikely to break and may not ever need replacing, but it may still be a good idea to keep a replacement part or two just in case.
3. Using wrong replacement parts
You’d think it would be easy to avoid this mistake, but with how common it is in the manufacturing industry, it obviously isn’t.
Not only does using the wrong replacement parts put the machine at risk for complete failure but it also increases the time with which it is inoperable. That said, it is crucial that maintenance personnel triple-check if the replacement part they’re putting in is the right one. To determine if the part is appropriate for the machine, technicians can use online portals and databases that contain bar codes, stickers, markers, and other details required when identifying the part to be replaced (since identifying information may be faded or removed completely due to age and wear).
4. Having a one-size-fits-all maintenance plan
Different machines have different specifications, which means a one-size-fits-all maintenance plan won’t work for each one. Some types of machines require little maintenance, while others require a high level of maintenance to stay in good condition. Maintenance plans should adjust accordingly in such a way that high-maintenance machines get the most attention and low-maintenance machines are not given more than necessary. With this type of approach, maintenance teams can maximize their resources while optimizing the performance of each machine.
5. Ignoring the manufacturer’s specifications
The machine manufacturer put their products’ specifications for a reason, and yet some plants choose to ignore them for the sake of higher production rates, even if it’s at the expense of their equipment.
Constantly exceeding the manufacturer’s specifications increases the wear and tear on the machine, which, in turn, leads to premature wear and tear. Of course, this also comes with a higher need for maintenance and, more often than not, more frequent and costly replacements.
To avoid problems for both operations and maintenance teams, operators must ensure that all machines are working under the manufacturer’s specification of usage amount, weight capacities, pressure, and other important specifics.
These mistakes are applicable to almost any machine in any industry, but they are the most common in the manufacturing industry in particular. Avoiding these mistakes does more than just keep machines in great shape; it is also crucial in reducing overhead costs, maintaining the safety of personnel, and maximizing the potential of each machine investment.