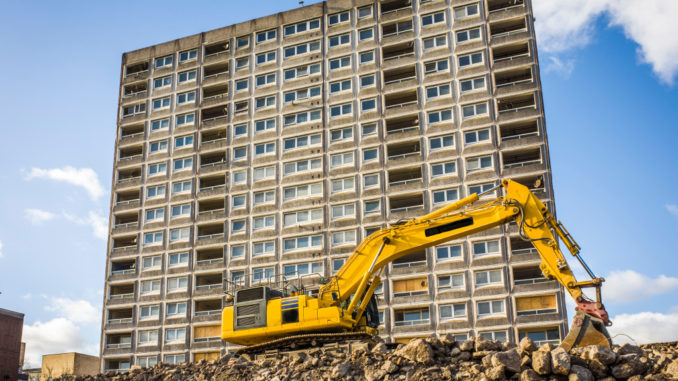
In the construction industry, excavation equipment is used for many jobs. These include landscaping for residential or commercial properties, prepping areas for road building, and excavating foundations.
Most of the time, both small- and large-scale excavators are used to dig out material. Excavation equipment is very important because it increases worker productivity.
However, an excavator can be very expensive, so it’s important to be aware of any problems that might arise to fix them before they become out-of-control issues.
Pay attention to the following:
1. Powertrain Failure
The powertrain is the collection of parts, like gears and belts, that power an excavator’s movement. Excavator powertrains are complex components because their power source comes from the engine. And since engines generate a lot of heat while running, powertrain components often fail due to high temperatures while working in hot weather.
A powertrain failure will cause an excavator to stop working. This will lead to a loss of power and power production.
Prevent powertrain failures by following the owner’s manual for service intervals or operating hours maximums. Also, ensure that powertrain fluids are clean and full before every usage.
Pay attention to powertrain components and watch for signs of wear such as loose belts, leaks, or grinding noises. These can usually be addressed before powertrain component repair and replacement is necessary.
2. Tracks Are Worn Out
The tracks that power an excavator’s movement are also vulnerable to wear and tear. When worn, the tracks will cause operating issues like reduced traction or loss of power.
These problems can lead to accidents that injure workers or damage equipment. Also, a loss of traction can cause a machine to slip and fall.
Tracks that become worn out need to be replaced immediately to avoid costly accidents. That’s why it’s important for excavator owners/operators to monitor their tracks regularly, checking for cracks or other damage. Make sure to keep the track tension even because an uneven tension may distort the track shape and damage it.
3. Vehicle Is Out of Lubricant
Every excavator has its own recommended lubricants for different parts. Examples include engine crankcase oil, PTO (power take-off) oil, and hydrostatic transmission fluid.
When any of these are used incorrectly or not at all, it can cause serious problems for the excavator. These include reduced engine power, damage to the engine’s pistons, and more.
Prevent these problems by following your excavator’s owner/operator manual for lubrication requirements. This is an ongoing process that needs to be done regardless of how often you use your excavator. Ensure the right type of lubricant is used for each part.
4. Overloads or Underloads
Manual excavators usually have a weight limit that shouldn’t be exceeded, while hydraulic excavators have an operating load limit at the end of the boom arm. If either of these limits is exceeded, it stresses the main components and can lead to several problems, including damage to the boom, arm, tracks, and engine.
This is an issue that can be dealt with if it’s caught early. If you notice any unusual sounds or vibrations coming from your excavator, stop using it immediately until you can determine the root cause of the problem. Also, make sure to regularly inspect your equipment for signs of wear or damage.
5. Hydraulic Leaks
Any hydraulic excavator is powered by a hydraulic system, which uses pressurized oil to power important components like the boom and arm.
A hydraulic leak happens when pressure is not maintained in the hydraulic system, causing low power output or a shutdown of that component. Furthermore, hydraulic leaks are dangerous because they can cause fires.
Therefore, an excavator owner/operator must check for hydraulic leaks immediately if he notices reduced boom or arm movement. Follow the advice in your owner’s manual for inspection intervals since different components require different timing.
6. Overheating Engine
All internal combustion engines produce heat during the process of conversion from fuel into energy. In the short term, this heat is dissipated efficiently by an engine’s cooling system.
However, over time as debris clogs up the cooling system and components age, overheating can eventually cause major damage to your excavator.
When an engine overheats, it slows down or stops working altogether. At its worst, it can even cause an explosion. That’s why overheating should always be taken seriously.
There are many reasons for engine overheating, including dirty air conditioners, broken thermostats, and low oil levels in the crankcase or cooling system. To prevent overheating:
- Remove dirt and debris from the engine compartment as often as needed
- Check for leaks in the cooling system
- Properly maintaining your equipment by conducting the recommended inspections and checks is usually enough to prevent these problems from happening
Regardless of the situation, it’s always a good idea to check your excavator for signs of damage after each use, especially if you notice any unusual sounds or vibrations.
As always, staying up-to-date with recommended service intervals and utilizing the best possible lubricants for your equipment is key. That way, chances are you’ll never have to deal with these types of problems.